LKAB digs even deeper for iron ore
2013-10-18 15:02:00
Summary:Sweden's LKAB opened its newest and deepest excavation level at its iron-ore mine in Kiruna in May, which is...
Sweden's LKAB opened its newest and deepest excavation level at its iron-ore mine in Kiruna in May, which is using an automated railway to move extracted iron-ore. Kevin Smith travelled 145km into the Arctic Circle and 1365m below the surface to visit the mine.
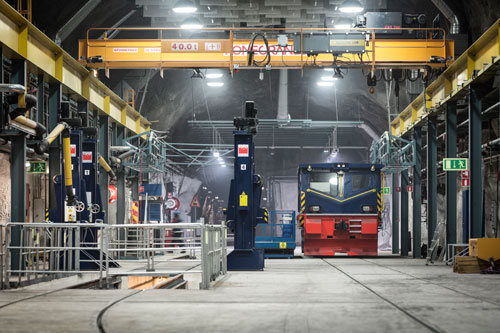
KIRUNA is a city on the move, quite literally. Built to serve and house the workers of Europe's largest iron-ore mine which towers over the city, continual excavation is affecting its foundations so much that the city is planning to relocate many of its major buildings before they are gobbled up by a huge sink hole.
The railway line, which runs north to Narvik in Norway and south to Lulea on the Baltic Sea, has already been relocated, meaning that trains entering the city from the south actually do so from the north. And with excavation continuing apace, further relocations are now essential.
Indeed Luossavaara-Kiirunavaara AB (LKAB) completed a SKr 12.5bn ($US 1.93bn), eight-year project to open up the mine's seventh excavation level earlier this year which guarantees operations will continue in Kiruna for at least another 20 years. Located 1365m below the original surface point of the mine which opened in 1888, production will slowly be ramped up in the next few years as excavations at the previous level, 1045m below the surface, simultaneously decline.
The project is LKAB's largest single ever investment, and Mr Hans Engberg, the company's general manager for projects, says full capacity at 1365m will be reached in 2017. At this point the mine will produce 100,000-110,000 tonnes of iron-ore per day with an annual capacity of up to 35 million tonnes, which is an increase from the mine's current capped output of 30 million tonnes.
An automated railway, as it did on the previous excavation level, is moving ore from the excavation point to a compressor where the ore is crushed before being hoisted to the surface.
"We performed a life-cycle cost analysis of five potential options, but a railway was preferred because we had to locate the compressor 1.2km away from the excavator due to potential stresses in the rock in that area," Engberg says. "The railway is the most efficient way of transporting ore over this distance."
LKAB is a 24-hour operation, with blasting taking place between 00.00 and 06.00, and extraction and removal from 06.00-00.00. A maze of dimly-lit road tunnels which descend at 10o°connect the mining levels and facilities in what feels like an underground city akin to Lang's Metropolis. 700 people work underground with air-conditioning maintaining a temperature of around 18oC on the new mining level which contrasts significantly with the often brutal arctic temperatures on the surface.
Around 90km of new tunnels were constructed for the new mining level, which required the extraction of more than four million cubic metres of rock. The new level accommodates an operations centre, offices, control rooms, and personnel space, with the deepest part of the mine now 1542m below the surface point.
Blasting
Once overnight blasting is concluded, the ore is collected by dump trucks which deposit it into 3m-diameter chutes to railway wagons situated directly below. Each train consists of 21 wagons with a combined capacity of 600-800 tonnes. The train is hauled by a locomotive supplied by Schalke, Germany, to a dumping station where it takes 2.5 minutes for the wagons to release their contents through the bottom of the wagon to the compressors situated below. From here the ore is sent to the surface via hoists which travel at 61km/h with each having capacity for 33.4 tonnes.
LKAB has installed 12km of track to serve the mine and three of its eventual 10 chutes are currently in operation with two trains in use, serving a single crusher and skip hoist. The track will eventually be extended to 15km to allow the mine to reach full capacity, at which point seven trains will serve 37 shafts, four crushers and five skip hoists.
Engberg says 1435mm-gauge was selected for the railway because it was found to reduce spillage compared with the existing 891mm-gauge infrastructure at previous mining levels. Sourcing replacement rolling stock components is also now a lot cheaper.
The locomotives are powered by a combination of 750V dc electrification and batteries. Nine production units have been ordered from Schalke and four service vehicles for various functions from Robel, Disab, Geismar and Zephir. Kiruna Wagon, Sweden, is supplying 120 wagons, with an option for up to 22 more, under license from Nordic Mine Technology (NMT), Canada, which supplied the first 21 wagons directly. When the new level is at full capacity seven locomotives will be in service at any one time hauling trains of 21 wagons with 16 wagons left in reserve or undergoing maintenance.
LKAB selected Midroc Electro in a contract worth more than SKr 360m in December 2010 to supply process control systems, power supply, electrical installation and control systems for the automated trains for the new mining level. Midroc subsequently subcontracted the railway element to Bombardier which supplied and installed the railway's automated operations system.
All of the trains are fitted with ATP while the nine operational trains will also be fitted with an Automatic Train Operation (ATO) system meaning that they are completely driverless. They are also utilising a variation of Bombardier's Interflo 150 CBTC solution which has been specially adapted for mining operations by offering automatic route setting, derailment detection at 42 locations and integration with the mine's ore loading and unloading facilities.
A centralised traffic control centre located on the surface manages the interlocking and radio communications for the railway and issues movement authority to the train. It can also provide on-demand operation when required. A second control centre is located in the mine at the production level which is used for redundancy purposes.
Moving block
Of course the major feature of any CBTC solution is its capability to offer moving block operation. Mr Valentine Paramasivam, Bombardier Rail Control Solution's global head of industrial and mining, says maximising capacity was a priority for LKAB and this is emphasised in the system rolled out.
It uses a CAB-display rather than signals to manage movements with 57 EBI Switch machines installed on the railway, and a system of 180 wayside balises used to determine train location. Balises inform the onboard odometer of the exact geographical location of the train, keeping the error in position provided by a tachometer to an acceptable level. In addition train position is reported by the train to the central interlocking every two seconds and not just when it passes the balises.
The system can accommodate more than 160 train pair movements per day, far in excess of LKAB's need for 143 with an average load of 650 tonnes which will reach its desired output of 35 million tonnes per year.
Paramasivam says LKAB's automated railway is a tried and tested solution having been successfully installed at Codelco's El Teniente copper mine in Chile since 1999. Interflo 150 is compatible with the WiFi radio system used in Kiruna and is adaptable to any radio system used by mines around the world. And with low-bandwidth demand it does not place any additional strain on an operator's network.
Paramasivam says that with 11% of the world's existing underground mining operations using railways, there is a strong market for train control solutions that will offer enhanced capacity in an environment where any time saved is money gained.
Freeport Indonesia is in the process of expanding operations at its open pit Grasberg gold and copper mine in the Papua Highlands of Indonesia, to a new underground mine where it will build a 28km railway. Midroc secured a SKr 550m contract for operations systems and again selected Bombardier as a subcontractor for the railway element.
It plans to install an identical system to that delivered to LKAB in Indonesia. And with miners in Australia, Africa, China and South America similarly exploring how they might improve the efficiency of their operations, and ultimately get more ore for their buck, LKAB is likely to become a reference point for more operations in the near future.
Key Words:LKAB,digs,even