复工了 高铁列车制造进行时
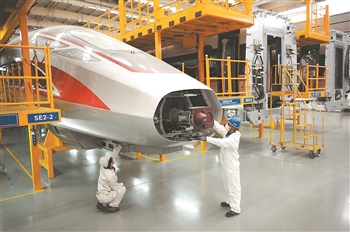
总装分厂的工人在车前端组装。
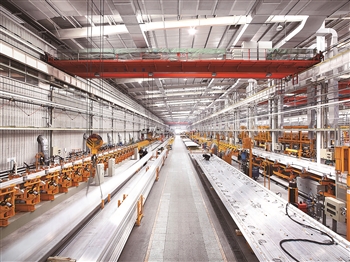
车体分厂生产线。
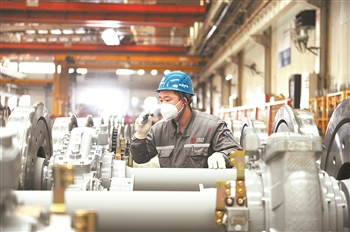
转向架分厂轮对组装完成后的初检作业。
在确保新冠肺炎疫情防控到位的前提下,复工复产关系到为疫情防控提供有力物质保障,关系到民生保障和社会稳定,关系到经济社会发展目标的实现。
记者的采访始于2月8日,以大型高铁制造企业为切入点。多家高铁制造企业的复工复产准备工作启动于2月5日,复工复产过程缜密,目前生产运转稳定,彰显了铁路和相关企业服务经济社会大局的一贯精神。
复工复产事关中国经济社会大局,2月下旬以来,与铁路密切相关的各高铁制造企业相继全面复工复产。高铁列车制造企业是怎么复工复产的?高铁列车特别是复兴号动车组是怎么制造出来的?
高铁车间的“彩排”
复工复产,对于制造业不是按下启动开关那么简单。
像高铁列车制造这样高技术含量的大型装备制造业,新冠肺炎疫情后的复工复产在制造现场进行得缜密,一如这个行业一贯细致、严谨的行事风格。
2月5日前后,中国高铁列车制造企业多数已经开始了复工复产准备。居家隔离的工艺人员、管理人员在电脑上形成复工复产方案,包括防疫措施、生产线工作量安排、制造流程、标准考核等多个方面的电子文档。这是复工复产的“设计图纸”,在网上传递、修改,最后经过多次网络会议讨论后方案定稿。
接下来是模拟演练。小部分人员组成演练小分队,在实地一次一次按方案演练。这个过程很像彩排,但是目标明确——发现方案中的漏洞以及可操作性不强的项点,强化、细化方案。
复工复产中防疫是核心,事关全局,而所有的企业都没有经历过,在没有经验可以依靠的时候,模拟推演是最快速有效的方法。
不同高铁制造企业都不约而同地将复工复产分为两个阶段:过渡复工和全面复工。
过渡复工多在2月10日后开始,为小范围复工,每日逐步增加工作人员数量,检验员工个人轨迹管控、个人防护、用餐、现场消毒以及应急处置等措施是否完善。措施的补强和完善每天都持续进行,比如现场消毒的最佳时间、进出餐厅的分流方法、物资配送怎么实现零接触……
2月20日前后,复工稳妥运行后,各高铁制造企业进入全面复工阶段。
复工复产了,又一批高铁列车正在被制造出来……
3个核心标配
21世纪工业企业的厂房是相同的味道,多是钢结构和彩钢板的组合,通常主体色是白色。大工业之下的新式厂房,外表平实,整齐统一,不追求特点。但是,在没有视觉特点、外表普普通通的厂房里,代表“中国制造”名片的高铁列车正在生产。
那些车间大门紧闭着,并有人严格检查进出人员身份。高铁列车制造属于国家级保密项目,制造现场的安保在装备制造业一直属于最高级别。
高铁列车到底是怎么造出来的?
在中国也是世界高铁列车产量最大的企业——中车青岛四方机车车辆股份有限公司一个个制造现场,答案以钢铁材质展示出来。
放下那些高深的技术,直观简单地说,高铁列车在制造中由四大部分组装而成:车体、转向架、车上下大部件、车内设施。
高铁列车的制造中,从时间上看,车体、转向架两部分同步进行,车上下大部件、车内设施同步进行。
车体制造在车体分厂进行,转向架制造在转向架分厂进行。车上下大部件、车内设施两部分常常被称为“总组装”,包括了检测和调试的内容,在中车四方股份公司这里,这项工作在总装分厂进行。
车体分厂、转向架分厂、总装分厂3个分厂,是所有高铁列车制造企业的标配,也是制造的核心部分。
3个分厂有各自成排的车间厂房,各自治理。但“三兄弟”总是尽量靠拢在一处,主要是为了方便成品的运输,因为他们制造的产品最终会集合在列车上。
车体分厂和转向架分厂因为都是以钢铁为原材料生产,这两个地方的制造场面都很“重工业”,天车和电焊火花让初来者一时难以适应。总装分厂就安静许多,几乎听不到噪音,是“白领环境”级的制造现场。
轻量化之“骨”
车体是个什么东西?车体就像是房子的框架,是高铁列车之“骨”,是高铁列车整车制造的核心技术之一。
在高铁列车的制造现场,车体的制造感最强。长达20多米的银色铝合金车体材料在各种工装上被不同角度地固定后,工人们穿着灰色的连体衣,戴着防护面具进行焊接。
铝合金是一种银灰的色彩,被切割后切口处有刀刃的光泽。世界高铁列车集体性地选择了这样的材料作为车体材料。
一个胖子想要跑得快会比一个瘦子困难一些。人们降低高铁列车重量的愿望越来越强烈,设计师们不由自主地想到了铝。铝的重量只有钢的1/3左右,可惜的是铝的硬度却低,这也是早期的高铁列车采用耐候钢材料的主要原因。
铝合金的出现,让铝不再“文弱”。铝合金是既瘦又强壮的“汉子”,这一材料迅速被用在高铁列车上。
高铁列车的重量降低,在行业语言里称为轻量化。
轻量化后不但利于提高速度,而且更为节能:因为重量轻可以少用电,因为重量轻也减少了对轨道的磨耗。
轻量化还有利于降低噪声,让高铁列车运行更为安静。
当初这些材料是进口的,现在高铁制造企业和国内铝型材专业厂家联合设计,全部实现国产化。在车体分厂门口,记者看到装载着不同铝合金型材的汽车在送货。
两车交会时会产生巨大的空气压力波,这个压力波主要由车体来承受。这时,车体首先要保证安全,还要保证气密性。
气密性的好坏,乘坐者会有直接的感受,飞机起落时内外压力差给乘坐者所带来的耳鸣和不适感,就与气密性直接相关。
高速下会车和出入隧道时,高铁列车容易面临气密性问题。为追求舒适,中国高铁目前的气密性指标设定为车内压力波动小于每秒200帕。这个数值小于飞机舱内的指标。
车体是列车的骨骼,是列车的主体,所有的部件都固定或悬挂在车体上。高速运行中,它不光承载旅客,它的强度还可以保护旅客。
一节车体上有70多种不同断面的铝合金型材,最薄的地方为1.5毫米,最厚的地方为4毫米。这种截面改变而强度不变的设计,不仅实现了减重,而且将车体气密强度提高到时速380公里时的6000帕。
下料,组合,成形。在3D打印到来之前,人类的所有工业品的产生都或明或暗地遵守这一思维方式和规则,这是现代制造的基本流程。
车体生产的过程是这样的:先将购进的铝合金原材料按尺寸切割,之后加工焊接成不同部件,这些部件被组合,最终组焊成一个车体。
中车四方股份公司车体分厂的动车组流水线厂房,银色的车体在这里一个一个地有序“出生”。在这里,每4小时完成1辆车体的生产。目前,中车四方股份公司有3条这样的生产线。
进门处你看不到生产线的布局,它们太为庞大了,而如果从高处俯瞰,会看到它是U型布局,自动化焊接机器人是生产线上的主力设备。车体中地板的组焊,由焊接机器人完成,机器人们平均每分钟焊接700米的总长度。
焊接机器人,看不到人的造型,只看到一台设备上多个焊枪在同时工作,而工人在观察和巡视。
在这里,车体加工的长焊缝全部由机器人完成,小的部位由人手工焊接。
焊接机器人的焊花,不是人操作时的断续状,而是持续地保持着强烈的、均匀的焊花,自动平稳向前移动。
焊接质量标准执行欧洲最严格的EN15085CL1级焊标准,焊接机器人的焊接质量由激光检测器同步跟踪。
铝合金焊接比其他焊接难度高,对焊接环境有恒温恒湿的高要求。为了保护操作者的健康,这里的厂房,顶部有数量惊人的空气净化设施。
每跨厂房之间有一个一米宽的通道,在这里,密集出现大量空气净化系统的送风口。形状不同、数量巨大、功用不同的这些出入风口,改善着制造现场的空气状态,对人对产品皆为有益。在老的火车制造现场,这种设施不多甚至是不存在的。
车体按结构形式分中间车和带驾驶室的头车两种。
中间车为基础车型,被分为底架、侧墙、车顶、外端墙、内端墙等几大部件分别焊接,这几部分基本同步开始制作,最后组焊成形。
底架就是列车地板处的那一部分钢结构。底架先进行正面焊接,之后是打磨,然后是底架反面焊接打磨。
端墙是车体的两端,块头最小,但是焊接量不小。车顶要先正面焊接,再反面焊接,主要由焊接机器人来担当。
侧墙是安装窗户的部位,面积不小,预留安装窗户的地方比较难操作。
将上面这些组合焊接在一起,一个车体就出现了。它是铝合金材质,体形巨大,那色彩和体形,有后现代的感觉。
最难的车体制造应该是头车的车体,也就是有驾驶室的车体。它主要是手工组焊,工艺更为复杂,尺寸要求更为苛刻……
在这里,双工位数控加工中心长60米,很容易吸引到你的注意力。这个用于车体侧墙和地板整体加工的装备,加工定位精度达到微米级,以保证车体的整体加工精度。
车体总组成焊接机器人,用于车体总组成时长直焊缝的焊接,同时兼具打磨、铣削、压紧等辅助功能。类似的许多非标设备都是中车四方股份公司自己研制开发的。
对于现代制造企业的实力考核,面积、产量、技术等级是考核之一,另有一个独特的测评指数:自制大型工装设备有多少?技术和工艺水准是什么?
私家秘制工装,已是企业之间比拼的秘密武器,制造现场拒绝拍摄。工装的技术保密被高铁列车制造企业看得很重。
车体焊接完成后,甚至是在焊接的过程中都在不断地进行调直打平,可以理解为对这个钢铁大家伙的精细修整,用的是打磨的方法。打磨几乎和焊接一样重要,目的在于消除应力,保证车身的平整度。
在车体分厂,最大的噪音来自于打磨工具启动后,砂轮和铝合金对撞时产生的声音。而且此时也有火花,这个火花常常比焊花喷射得更远。
整个车体分厂在视觉和听觉上,都是“火热”的场面:铝合金的长大部件在空中吊运,长达几十米的装备、焊花、噪音、穿着如太空服一样的防护服的工人们……
这个空间看上去并不整齐划一,却隐含着如齿轮咬合一样明确的次序与流程。
人在其中,因无法听清别人的话语而自然减少交谈,所以在绝大多数时候,是你一个人在独自感受。大工业的强硬、操作者的辛劳、中国制造的优势和气场……林林总总,慢慢过来深重地包裹你。
当车体制作完成后,涂装工艺开始。车体前后要多次上腻子,底漆和面漆的喷涂也是多次,最后全身白色的车体呈现。那个银色的车体看不到了,变成了我们在站台上看到的那些白色的列车车身。
这时候,车体还是没有轮子,它被气垫船送进总装分厂。
车轮的力量
另一侧的厂房是转向架分厂,转向架的制造在同步进行。
转向架是列车的“脚”,对于以运送为天职的列车来说,它的重要性不言而喻。这是一个外形很像小车的部件,主体是4个车轮2根轴1个钢铁框架,这个框架的行业名称是“摇枕”或“侧架”,总体称为“构架”。
转向架分厂的工业气势一点不比车体分厂弱,虽然转向架的体形要比车体小了太多,但它的确是太关键了。
高铁列车车轴是空心的。那么高速之下,这个快速旋转并承载列车的部件竟然是空心的,的确是让人吃惊。
车轴生产采用中央控制模式,自动上料、加工、检测、下线,中心孔偏移量误差小于等于0.1毫米。加工线整线封闭,加工的过程中看不到钢屑飞溅的现象。中车四方股份公司的空心车轴自动化生产线,仅有2名操作工人。
车轴加工完成后,与车轮组装成轮对。
转向架的构架,好比是整个转向架的“骨架”,其重要性如同人体的躯干一样,制动系统和牵引系统均安装在构架上。
从高处向下拍摄转向架构架自动焊接生产线,会为其密集有序而惊叹,它的规则与细致,又让你怀疑是否身处在一个焊接生产厂房中。
全长120米的生产线,5台焊接机器人、2条自动运输线,重量不轻的构架在流水线上如同一个小玩具一样被传送、焊接、翻转、输出。
每天,这里出品的构架,多数焊缝都是由焊接机器人自动焊接完成,焊缝的一次探伤合格率可以达到98%以上。
构架焊接完成后有复杂的涂装过程,也就是油漆。
沿着设定的轨道,一个个构架像一件件工艺品陈列在吊架上,从入口进去,穿过U形通道,在完成一个个自动进行的复杂工序后,出来时已做好了防锈和表面涂装,构架很光鲜漂亮了。
之后开始转向架的组装,即制动装置、电机和各种管线的安装。高铁列车的电机等重要部件也会安装在转向架上。
组装中,在专用工艺装备的帮助下,构架分正反两面安装。这边安装完毕,被快速准确地翻转180度。因为使用全套的定制工具,部件的安装有序、精准。最后,安装了多种部件的构架,被吊起落在轮对上,转向架装配完成。
组装完成的转身架,要进入综合试验平台,在那里接受各项检测,数据合格后等待装车。
安静的总组装
总装分厂比前面两个分厂的厂房面积更大,却十分安静,高端大装备工业的气息在这里强烈呈现。
这里厂房连着厂房,一列列白色的动车组车体在这里排列,黄色的安装台位包围着它们。在这里,车体、转向架及高铁列车车上车下大部件、车内设施,即对每列车的4万余个零部件进行集成及调试。这里,是高铁列车制造的核心之地。
相对于转向架、车体的自动加工、自动焊接,总装的大部分工作需要人工或半人工方式完成。工人的操作技能对于保证总装质量至关重要。总装分厂的员工一年中要多次接受培训。
在总装分厂,工作者的面孔都很年轻,30岁左右的占绝大多数。他们多是在2004年后进入这里,10多年中与高铁一起成长。
组装现场有成排的黄色工作台位,它们是总装分厂里色彩最为醒目、数量最多的设施。每个台位的端部都有一个显示生产状态的LED显示屏,显示绿色表示生产正常,显示红色表示异常。
动车组电线下料区是让人印象深刻的地方,因为这里是“抽象画”工作区。动车组每列车约1万多根电线电缆,必须准确无误地可靠连接。电线下料区,以白色背板模拟现实车辆按1∶1下线,然后对电线电缆成束捆扎。日常生活里一个耳机线也能乱成一团的情形常常出现,1万多根电线电缆在这里却整齐有序,配线的错误率仅为0.025‰。一束一束的电缆,之后被安装在车上。
在总装分厂,白色的车体被架在台位上,自然地分为车上、车下和车顶3个工作区,一节车上有多个部门的人员在同时工作。
车上安装的是防寒材料、地板、风道、车窗、座椅、装饰件等,车下大部件主要是变压器、变流器等,车顶主要安装受电弓和主电力线,高铁列车在这里被彻底武装起来。
之后,工人们请出已做好的转向架,将车体吊装上去,称为落车。
落车的过程颇为惊艳,场面很大,因为车体本身不小;这时候总是有一种愉快,因为即将进入完工。
落车完成的车辆,进行单车的称重、淋雨、保压、耐压和气密等一系列试验。
任何车辆的制动都是至关重要的,跑得很快的高铁列车的制动就更为重要。管路的密封性决定着空气制动的有效性,国家标准和欧洲标准都允许管路有一定的泄漏量,空气制动气密试验的企业内控标准为管路保压15分钟泄漏零,保证空气制动的有效性。
试验合格后,进入调试阶段。一节一节连接起来、网线极多、电脑控制的高铁列车的调试可以称为是一项工程。这项工程内容繁多,常常延续半个月至一个月之久。首先是单节调试,然后是编组调试,编组调试又分静止调试和动态调试。这个过程极为安静,调试人员多是依靠笔记本电脑来工作。最后,高铁列车在环形试验线上进行动态试验,相当于试跑。
调试完毕,高铁列车已完全具备上线条件,全新的高速动车组列车等待调度命令,出了厂区的专用线进入运营线路,开始自己的旅程。
2020年2月,高铁列车制造企业全面复工复产,时速350公里的16辆长编组复兴号动车组CR400AF-A型和超长版的17辆编组复兴号动车组CR400AF-B型,在中车四方股份公司高速动车组生产线上投入了生产制造。
春天,等待着复兴号高速动车组。